Aircraft Corrosion Prevention And Control Strategies
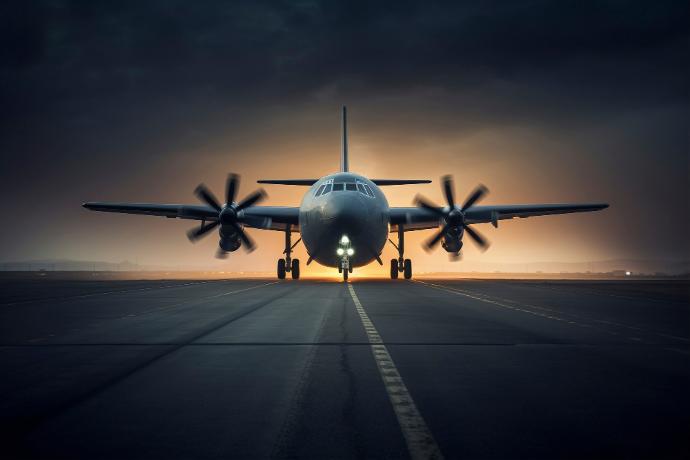
Aircraft, designed for optimal power-to-weight ratios, face a significant challenge in ensuring longevity and safety in the face of corrosive environmental factors. The corrosive deterioration of critical surfaces poses a threat not only to the aircraft's performance but also to human lives. In this blog, we delve into the various aspects of aircraft corrosion prevention and control strategies, emphasizing the importance of careful material selection, coatings, and maintenance procedures.
Common Types of Aircraft Corrosion:
Corrosion on aircraft surfaces can manifest in different forms, with crevice corrosion being one of the most common. This type of corrosion accelerates in the presence of environmental catalysts, leading to the formation of oxygen differential cell corrosion. Other forms, such as stress corrosion cracking and exfoliation corrosion, can affect structural integrity and mechanical parameters. Recognizing these corrosion types is crucial for effective prevention and control.
Techniques of Corrosion Control:
To combat corrosion, aircraft design must involve comprehensive corrosion control planning. Material selection, coating and surface finish choices, moisture drainage systems, joint sealants, and the use of corrosion-inhibiting chemicals all play pivotal roles. A well-thought-out corrosion prevention program, coupled with effective maintenance and corrective action plans, ensures the longevity of the aircraft.
Areas Prone to Corrosion Damage:
Aircraft components, especially those exposed to corrosive environments, require meticulous inspection. Reciprocating and jet engines, exhaust areas, rivet heads, landing gear, and battery compartments are among the vulnerable areas. Regular inspection, cleaning, and maintenance are essential to identify and address corrosion in a timely manner.
Metallizing and High-Temperature Coatings:
Aircraft engines, operating at high temperatures and velocities, demand advanced coatings to minimize corrosion and metal loss. Techniques such as high-velocity oxygen fuel spraying (HVOF) and plasma spray, along with ceramic matrix composites, are employed for critical engine components. Barrier coatings and ceramic coatings offer superior resistance to high-temperature cycles and corrosive environments.
Requirements of Top Coatings and Primers:
The coatings used in aviation, whether for military or commercial aircraft, must adhere to stringent standards. Urethane, polyurethane, acrylic urethane, and epoxy coatings are commonly used, each with its advantages and specifications. The choice of coatings depends on factors like durability, chemical resistance, gloss retention, and application requirements.
Conclusion:
Protecting aircraft from corrosion involves a multifaceted approach, from careful material selection to advanced coating technologies. Regular inspections, preventive maintenance, and the use of high-quality coatings contribute to the economic service life of an aircraft. In an industry where safety and reliability are paramount, implementing robust corrosion prevention and control strategies is not just a necessity but a responsibility that aviation professionals must uphold.