Different Types Of Aircraft Engines
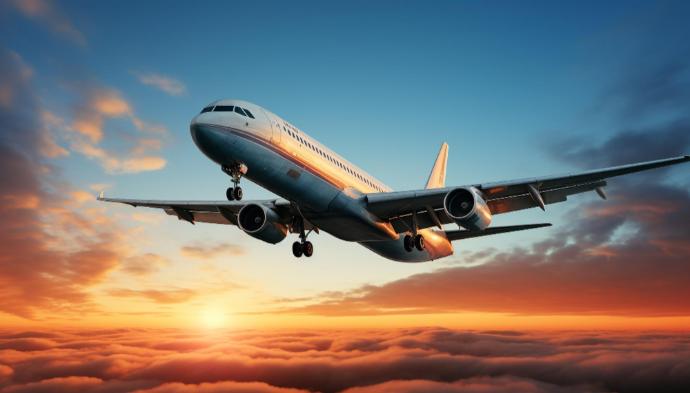
From the Wright brothers’ first flights to today’s transcontinental journeys, propulsion has always defined what aircraft can achieve. Over time, engineers have refined aircraft engine types to meet demands for greater speed, higher efficiency, and quieter operation. Understanding the main types of aircraft engines helps pilots, operators, and enthusiasts appreciate how powerplants shape every journey and why choosing the right motor matters.
The Piston Engine
In aviation’s early history, piston engines borrowed heavily from car technology. Early models mixed air and fuel in cylinders, then ignited the mixture to push pistons and turn a crankshaft. Rather than driving wheels, that crankshaft spun one or more propellers to generate thrust. For nearly four decades after Wilbur and Orville’s 1903 flight at Kitty Hawk, every airplane relied on piston-driven props.
Today’s small general aviation aircraft still favor piston designs for their simplicity and affordability. At light power settings, piston engines deliver excellent fuel economy and low purchase price. However, as aircraft grow larger, piston units struggle to produce enough power without an increase in size and weight, making them impractical for heavy transports or high-speed travel.
The Turboprop Engine
Turboprops emerged in the 1930s and entered widespread service by the late 1940s. They combine turbine technology with a propeller in which air is compressed, mixed with fuel, and ignited, then its high-energy exhaust spins a turbine that, through a gearbox, turns the propeller at efficient speeds, typically 250–400 knots.
Because they create more energy from combustion than normal pistons, turboprops are best suited for aircraft operating at moderate altitudes and shorter runways. Regional airliners and cargo planes often use turboprops for their fuel efficiency and climb performance. On the downside, the gearbox adds weight and maintenance challenges, and turboprops can’t sustain the high cruise speeds that pure jets achieve.
The Turbojet Engine
The turbojet can be considered the first true jet engine. Air enters the intake, then moves through compressors, a combustion chamber, and turbines in sequence. Instead of turning a shaft, the hot exhaust blasts rearward at supersonic speed, creating thrust directly.
Turbojets revolutionized travel by making it possible to hit unprecedented speed and altitude. Early airliners like the De Havilland Comet and Boeing 707 depended on turbojets to cut down journey times. Yet, their simplicity comes at a cost as they require high fuel burn, make turbojets costly to operate, and produce more noise compared to later designs.
The Turbofan Engine
Turbofans evolved to combine turbojet thrust with fan-driven bypass air. A large front-mounted fan pushes most incoming air around the core combustion path, also known as the bypass stream, while a smaller portion feeds the compressors and burners. By bringing together these streams help in bringing about higher thrust with lower fuel consumption and much reduced noise.
Today’s commercial jetliners almost exclusively use turbofan engines. By varying bypass ratios, engineers can tailor engines for long-haul efficiency or short-takeoff power. The quiet hum of a high-bypass turbofan is the signature sound of modern airports, finding the balance between efficient performance and environmental concerns.
The Turboshaft Engine
Turboshafts mirror turboprops but drive shafts instead of propellers. Built to turn transmissions, they power helicopters’ rotor systems. Unlike fixed-shaft prop engines, a turboshaft’s gas generator and output rotor spin independently, allowing consistent rotor speed even if the engine RPM fluctuates.
Helicopters rely on turboshafts for their compact size, light weight, and strong power delivery. Whether lifting emergency medical teams or ferrying passengers to offshore platforms, turboshafts allow vertical flight profiles that no other aircraft engine types can match.
Choosing the Right Engine
Performance and Need
Selecting between pistons, turboprops, turbojets, turbofans, or turboshafts depends first on how you plan to fly. Short hops at low altitude favor piston or turboprop power. Long-distance, high-speed runs call for turbines, turbofans for airliners, turbojets for niche speed champions, and turboshafts exclusively for rotorcraft.
Fuel Efficiency and Operating Costs
Fuel price often dominates an operator’s budget. Piston engines shine at low power settings; turboprops follow at midsize ranges; and modern high-bypass turbofans win out on long-hauls. Turbojets, while fast, usually lag in economy. Understanding these trade-offs keeps operators profitable and sustainable.
Maintenance and Supplier Network
Engine reliability hinges on proper servicing and access to quality components. A trusted aicraft parts supplier like GFA can provide original-equipment parts, overhaul support, and timely inventory, critical for minimizing downtime. Whether sourcing piston cylinders or turbine blades, partnering with a supplier that understands each engine’s quirks ensures smooth operations.
Innovations and Future Trends
Hybrid and Electric Propulsion
As battery energy density improves, hybrid-electric systems are moving from concept to flight tests. These architectures pair small turbines or pistons with electric motors to boost efficiency on climb or taxi phases, promising lower emissions and quieter operations.
Sustainable Aviation Fuels
Beyond hardware, fuel chemistry is evolving. Bio-derived and synthetic fuels blend smoothly into existing turbine engines, especially turbofans, to reduce carbon footprints without making many modifications to current fleets. The rise of new fuels with hybrid powerplants might open a greener path forward.
Conclusion
From humble piston-prop designs to the intricate bypass streams of modern turbofans, the types of aircraft engines on today’s runways reflect decades of innovation. Each powerplant, piston, turboprop, turbojet, turbofan, or turboshaft serves a unique mission, balancing power, efficiency, weight, and noise. By grasping these differences and working with a reliable aircraft parts supplier, operators can match engine capabilities to operational needs, ensuring safety, performance, and cost-effectiveness in the skies.